Procurement, safety and the culture of the construction industry
Professor David Mosey is at King’s College London, and is Director of the Centre of Construction Law and Dispute Resolution. David Sawtell is at University of Cambridge and is a barrister at Lamb Chambers.
Posted
Time to read
The safety of the future occupiers should be a paramount consideration when residential properties are built or renovated. The Grenfell Tower fire, and other fires and construction failures both before and after that tragedy, demonstrate that on a number of occasions this has not happened. The decisions that determine the design and construction of these buildings and that directly affect their resulting safety and quality are made long before the works begin. How do we ensure, then, that safety, and not only cost, is the driver behind these decisions? Traditional approaches to procurement and contracting emphasise the initial build cost and not the value delivered across a structure’s whole life, and are not the best way to promote improved safety.
Criticisms of traditional procurement strategies
Following the Grenfell Tower tragedy Dame Judith Hackitt produced her Interim Report on Building a Safer Future: Independent Review of Building Regulations and Fire Safety in December 2017. She was clear in her foreword that the entire system of regulation (including the different people working in it and how the various parts interact) needed to be re-evaluated: “Changes to the regulatory regime will help, but on their own will not be sufficient unless we can change the culture away from one of doing the minimum required for compliance, to one of taking ownership and responsibility for delivering a safe system throughout the life cycle of a building.”
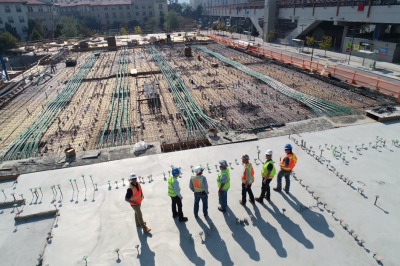
This concept of culture change was developed in Dame Judith’s final report, Independent Review of Building Regulations and Fire Safety: final report, promulgated in May 2018. She attacked the current system of safety in the construction industry where: “the primary motivation is to do things as quickly and cheaply as possible rather than to deliver quality homes which are safe for people to live in.” Chapter 9 of her report, focusing on procurement and supply, noted that: “The procurement process kick-starts the behaviours that we then see throughout design, construction, occupation and maintenance.” The report identifies that a number of fire safety issues are exacerbated by last minute contractor appointments under tender competitions and contract forms that prioritise low-cost solutions: ultimately, these practices “provide poor value for money and poor building safety outcomes.”
What are the problems with a traditional route to construction procurement?
In practice, there are two common forms of ‘traditional’ construction procurement in widespread use: firstly a construction contract where the design is created by an agent of the employer such as an architect, and secondly a design and build contract, where the contractor takes on design and construction responsibilities. Both forms are based on a lump sum price provided by the contractor in response to the employer’s brief and followed almost immediately by mobilisation for work to start on site. These traditional procurement models do not provide for a conditional appointment period ahead of start on site during which the employer and contractor, and the design consultants and key subcontractors, can ensure that they agree with each other’s design, cost and risk assumptions. In what is called a single-stage tender, with price often being the determinant factor in the selection of the winning contractor, there is very limited opportunity for that contractor and its subcontractors to make recommendations in relation to the design solutions required by the employer and its design consultants: this is discussed further in Chapter 3 of David Mosey's Early Contractor Involvement in Building Procurement: Contracts, Partnering and Project Management.
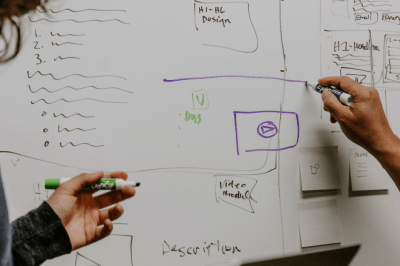
A number of criticisms of these widely used approaches to construction procurement and contracting have been made, both in the Hackitt Final Report and elsewhere:
- The contractor has very little input to the design and ‘buildability’ of the structure.
- It places the emphasis on a low initial price, rather than quality or value throughout the lifecycle of the built structure.
- Rather than the employer and the contractor becoming partners in a project, they are set up as antagonists, leading to “claimsmanship” and opportunism, especially if there are unforeseen circumstances leading to changes in the work.
- There is very little opportunity for stakeholders such as residents and other users to become involved in the design and programme planning of the works.
None of these criticisms are new; they have been identified in a series of government reports on the industry since at least 1962. The call for dramatic improvements in the procurement of construction operations, grounded on integrated relationships based on measured performance, is something that must now be acted on, as discussed by David Sawtell here.
What is collaborative procurement?
Collaborative construction procurement has been described by David Mosey in Collaborative Construction Procurement and Improved Value as “a set of processes and relationships through which teams can develop, share and apply information in ways that improve the design, construction and operation of their projects”.
Sir Michael Latham in his 1994 report, Constructing the Team, identified that one feature of a construction contract suitable for modern conditions is that it includes: “Firm duties of teamwork, with shared financial motivation to pursue those objectives.”
There are a number of recognised hallmarks of collaborative procurement and contracting:
- Early involvement with all those who have a value contribution to make, such as specialist contractors. For example, research by King’s College London led to guidance on using a two-stage form of procurement, with the contractor heavily involved in designing to develop an early project brief and in tendering subcontract packages under its own early conditional contract before the works are finally priced and approved for start on site (Project Procurement and Delivery Guidance: Using Two Stage Open Book and Supply Chain Collaboration).
- Selection of team participants by value, taking into account quality, prospective whole life costs and improved social benefits.
- Adopting commercial arrangements that underpin collaborative principles, using consistent appointments across all team members with agreed mutual deadlines, joint decision-making, early warning and joint risk management as set out in the PPC2000 and NEC4 contract forms.
- Adopting client-focused key performance indicators linked to incentives such as shared savings and the prospect of future work.
- Utilising teams that have learned to work together by using frameworks and other long term call-off contracts rather than tendering every project individually.
(see, for example, the Constructing Excellence Hymn-Sheet).
How can collaborative procurement support safer buildings?
The recommendations and proposals advanced by Dame Judith Hackitt “can all be addressed through the commitments and relationships established in a collaborative procurement model”, as David Mosey stated in Collaborative Construction Procurement.

The Housing Forum’s June 2018 report, Stopping building failures: How a collaborative approach can improve quality and workmanship made a series of recommendations. One of its central messages is that clients should procure for value, not necessarily by selecting the lowest price, but by assessing what reduces costs over the life cycle and increases performance and quality. It encouraged those considering engaging in construction operations to consider alternatives to single-stage design and build contracts: instead, the report authors urged clients to engage in tender processes that would see them “moving away from traditional single-stage competitive tendering”. It also highlighted that appropriate framework agreements such as the FAC-1 framework alliance contract can link together a series of housing capital investment programmes in order to share improvements and efficiencies.
The £13m refurbishment of Rogate House in the Nightingale Estate in Hackney provides an early example of how a collaborative approach to procurement delivered on these recommendations. The project saw a level of involvement and support from residents that was not apparent in an earlier scheme. The PPC2000 form of collaborative contract established a joint basis for the development of designs and risk management: for example, concrete and asbestos specialists were appointed at an early stage to analyse design solutions. The construction phase timetable was advanced on the basis of resident consultation. Rather than emphasising cost over value and safety, the early agreement of contractor profit and overheads enabled deeper analysis of other cost information and allowed change and risk to be managed without dispute: Association of Consultant Architects, 10 years of Partnering Contracts.
Prioritise value and safety, not cost
The procurement strategies and contracting processes introduced above are not new. They have been tested on billions of pounds of procurement in the UK alone, and have been adopted in a number of countries across the globe. Traditional forms of procurement with an emphasis on price and blame exacerbate other problems in the whole system of the procurement of safe structures. Changes to the regulatory regime alone will not work: instead, we need to ensure that our procurement and contracting strategies support the construction of safer buildings.
__________
How to cite this blog post (Harvard style)
Mosey, D. and Sawtell, D. (2019). Procurement, safety and the culture of the construction industry. Available at: https://www.law.ox.ac.uk/housing-after-grenfell/blog/2019/12/procurement-safety-and-culture-construction-industry (Accessed [date])
Keywords:
Share
YOU MAY ALSO BE INTERESTED IN